Today, environmental consciousness is a priority in many industrial sectors, including the road construction industry. To meet these needs, there is a growing trend towards using road plates made from recycled materials.
This process involves injecting processed plastics into suitable molds, resulting in durable and environmentally friendly products. Our company has made significant improvements in the production process by comparing it to traditional plastic injection methods. We have introduced a sequentially operated, multi-point hot runner system that has enabled us to reduce production time by 15% and decrease energy consumption. In this article, we will take a closer look at this process.

The Bole 2300 injection molding machine.
The first step in the process is preparing the appropriate plastic mixture, typically in the form of granules or flakes. This recycled material can include various types of plastics, such as polyethylene (PE), which are carefully blended in the correct proportions. Our extensive experience has allowed us to develop a recipe with excellent technical parameters.
- The first step in the process is preparing the appropriate plastic mixture, typically in the form of granules or flakes. This material is sourced from recycling and includes plastics such as polyethylene (PE), which are carefully blended in the correct proportions. Our extensive experience has allowed us to develop a recipe with excellent technical parameters.
- Next, the prepared plastic is heated and injected under pressure into a mold that has the desired shape of the road plate. This mold is precisely crafted from steel
and aluminum alloys to perfectly match the designed pattern and size of the plate. - After the plastic is injected, the process moves on to the cooling stage. Water or other cooling agents are used to rapidly cool the plastic in the mold, allowing it to harden and take on the desired shape of the road plate.
- Once the cooling process is completed, the mold is opened, and the finished product is removed. The entire process is automated, and a specially programmed robot precisely transfers the product onto a pallet. The road plate now has its final shape and is ready for use.
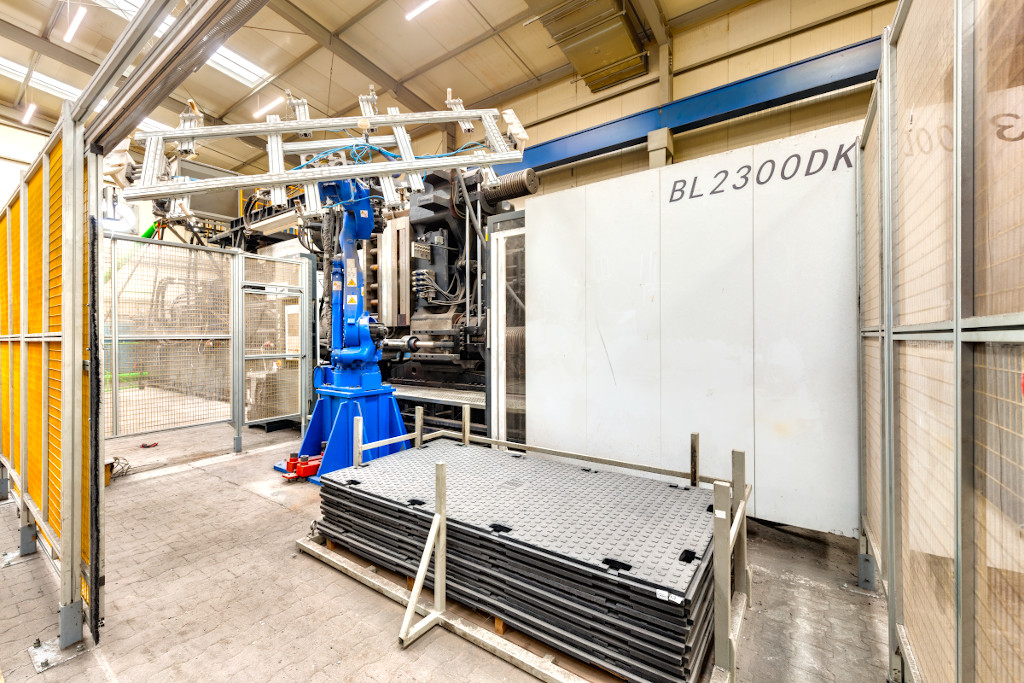
- Next, a quality control inspection is carried out on the manufactured plates to ensure they meet all design requirements and quality standards. Products that do not meet these criteria may be rejected or subjected to further processing.
- The finished road plates made from recycled plastic are delivered to construction sites or projects. They are used as temporary surfaces in various projects, ranging from roadwork to construction site setup. Thanks to their durability and resistance to weather conditions, they provide an environmentally friendly and efficient solution.
The production of road plates from recycling is an excellent example of using modern technology to protect the environment and create durable products for the construction industry. It is also a way to reduce waste and reuse it for construction purposes, which has a positive impact on our planet.